When forming shorter cases from long parent cases, a good portion of brass must sometimes be removed from a newly elongated neck, as in making .22-250 Remington cases from .30-06 brass. This same long-neck situation may come about when forming various wildcat cartridges. Sometimes .30 or .40 inch of neck must be removed; too much to take off with a conventional case trimmer.
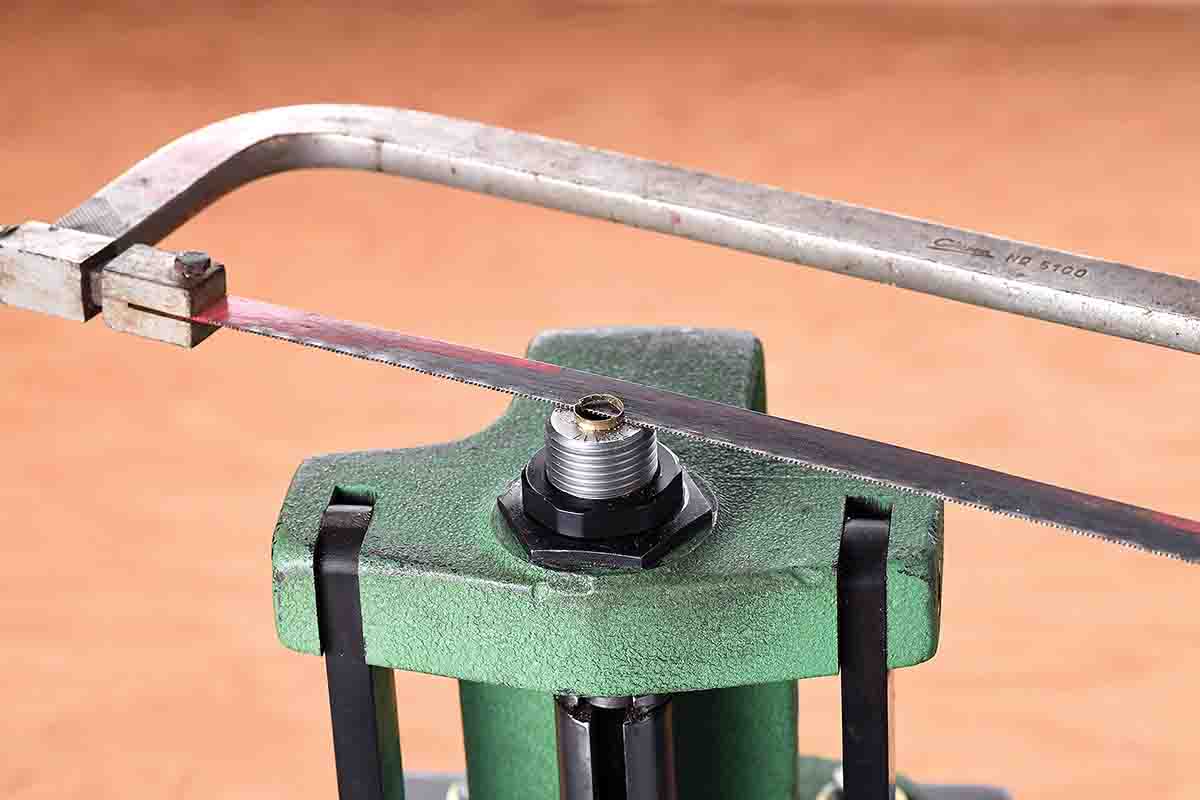
Above, RCBS makes a case forming die. The case is run into the die until the shellholder contacts the bottom of the die. The case protruding above the die is then cut off. Below, after using a hacksaw to remove the bulk of the brass, a bastard file is used to remove the rest, making it flush with the top of the die.
RCBS makes a case forming (form-and-trim) die for the purpose. The top surface of this die is file-hardened so that neither hacksaw teeth nor file will cut into the die metal. In use, the die is threaded into a conventional loading press so that a shellholder contacts the bottom of the die when the ram is at or near the top of the stroke. Then the ram forces a properly lubed case all the way into the die, forming it. The case neck extending above the die is cut off with a hacksaw as close to the
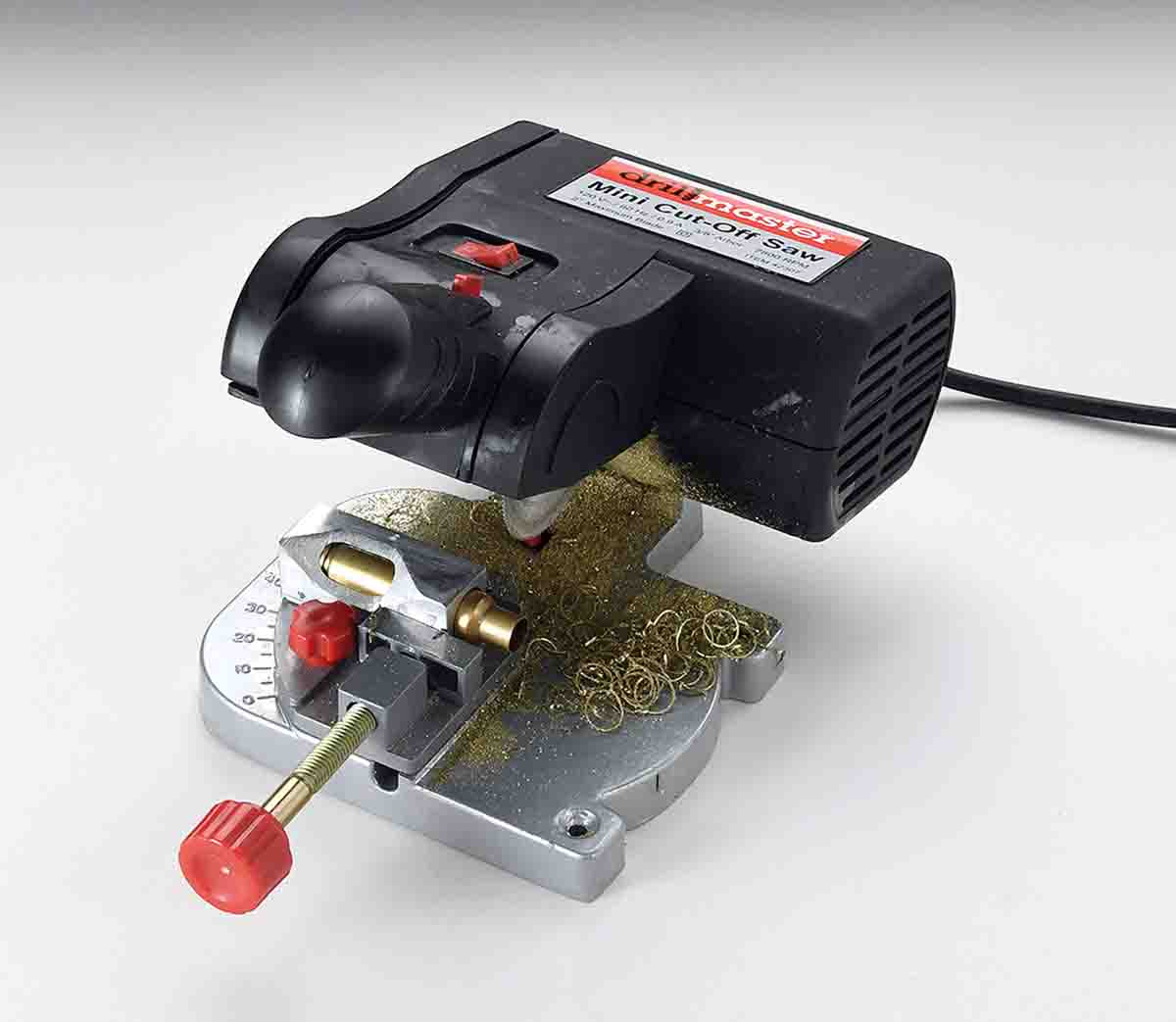
The small, inexpensive Mini Cut-Off Saw is available from Harbor Freight. It takes a circular blade 2 inches in diameter.
die as possible. Next, the remainder of the brass is filed flush and smooth with the top of the die. The case mouth is then chamfered inside and out, and the neck is reamed or turned if necessary.
Years ago, the late Fred Huntington, founder of RCBS, gave demonstrations wherein he illustrated the use of the form-and-trim die. One quick, smooth swipe with a sharp hacksaw blade can remove the bulk of the brass, with the cut-off neck flying across the floor. That operation is impressive to an audience not used to seeing it done. (Fred was a great showman.)
The process results in a square neck after filing flush. You can even use the method as a case trimmer if you want. If the case is run all the way into the die, it will be trimmed to the correct length.
The down side is that when there are a lot of cases to cut and file, it takes a fair amount of time and filing effort; enough that your hands and wrists can tire. After using various form-and-trim dies to shorten thousands of cases over the years, I found a better way.
Harbor Freight sells a DrillMaster Mini Cut-Off Saw with a 2-inch blade for about $35 that is great for cutting brass case necks,
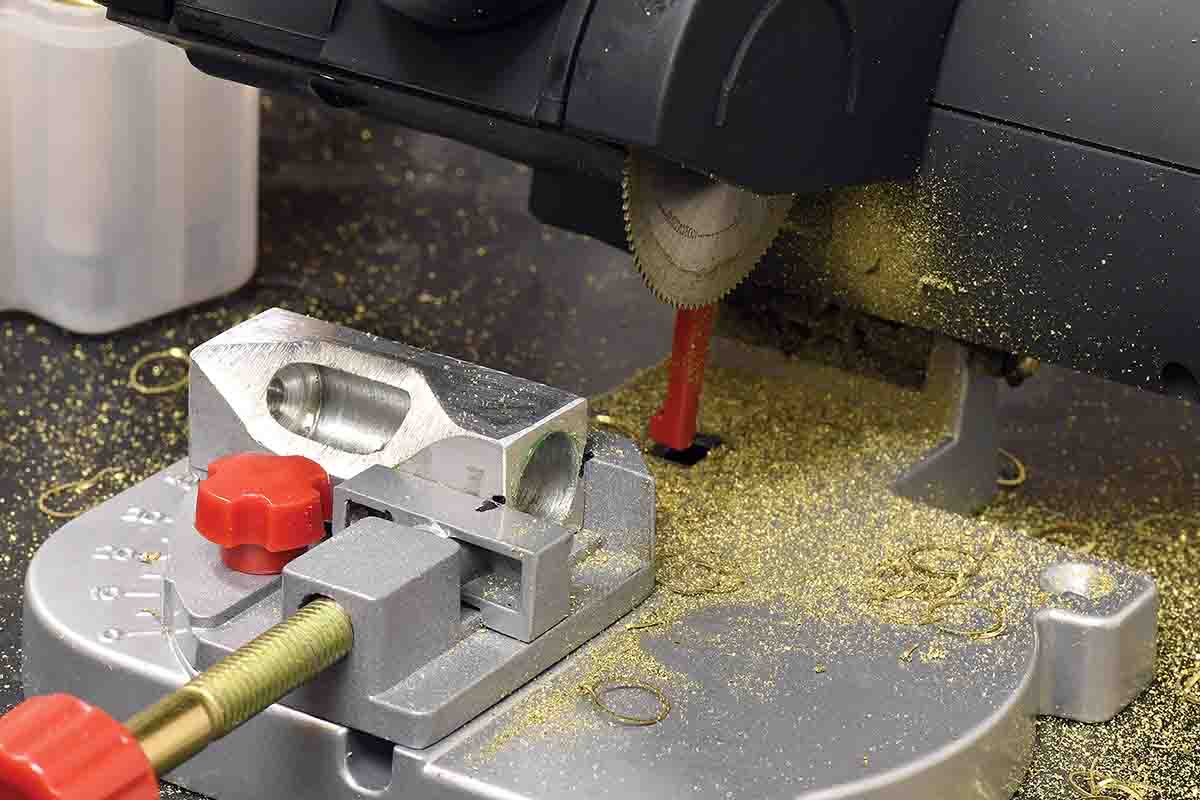
The aluminum block shown is from Myers Fabrication as placed in the saw’s vise.
and it comes with a built-in vise. The unit is made of lightweight material not intended for heavy duty work; it is perfect, however, for cutting case necks. The problem is that the vise is not ideal for holding cases, nor does it have a means for case length repeatability. Enter handloader Wayne Myers who made a case-holding fixture for his own use, cutting .223 Remington cases to make .300 AAC Blackout brass. His fixture is a small aluminum block machined as shown in accompanying photos. A hole of the proper diameter is drilled to depth lengthwise in the aluminum. A case is dropped base first into the bottom of the block’s cavity. The block with case is slid laterally between the saw’s vise jaws until the proper cutoff length is attained. The block is then clamped in the vise jaws.
In use, finger pressure on the side of the case exposed through the window keeps it firmly seated at the base of the internal cavity. The high-speed saw is then started and the blade lowered onto the case neck, cutting it quickly and cleanly. The trimmed case is pulled out of the block, another is inserted and the sawing action is repeated. Once adjusted, it is fast and easy to cut cases. It makes no difference the length of the brass to be removed; the time required is the same.
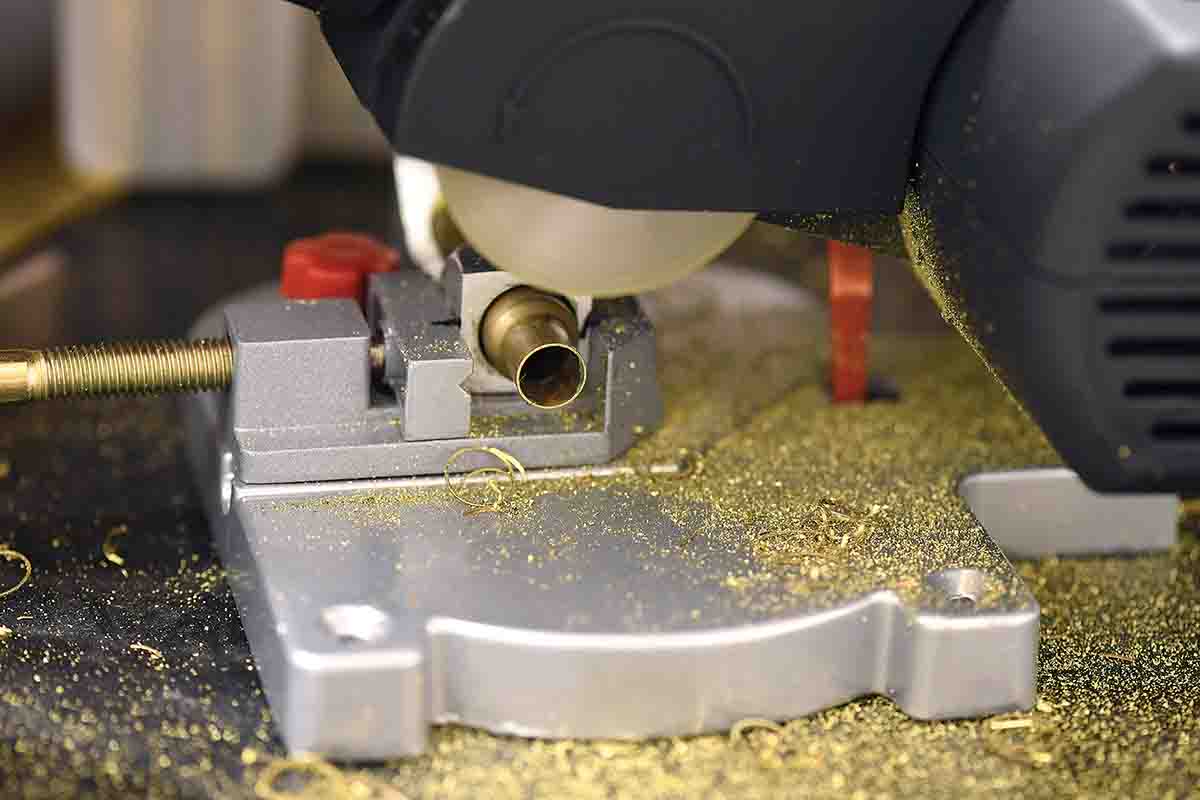
The fine-tooth saw leaves a smooth surface with almost no burrs. When the case is cut it is slipped out of the block and another is slipped in for cutting. It is fast to use.
I checked mouths for squareness by putting some sawed cases into a form and trim die that I had been using. The case mouths were as square as those made in the form-and-trim die. The Mini Cut-Off Saw cuts so cleanly that I started using it for simple trimming operations where only a small amount of brass is removed. The blade’s teeth are so sharp and fine that it removes even a thin donut of brass without burrs on the case mouth.
Accompanying photos show the case-holding fixture and how it works. If you do not want to go to the trouble of making a case-holding block, contact Myers Fabrication, Inc. at 90020 Prairie Road, Eugene, OR 97402 or wmyers@myersfab.com. The cost is $19.99 for any conventional rifle or handgun case diameter. He is now making blocks with a screw/bolt adjustment in the base
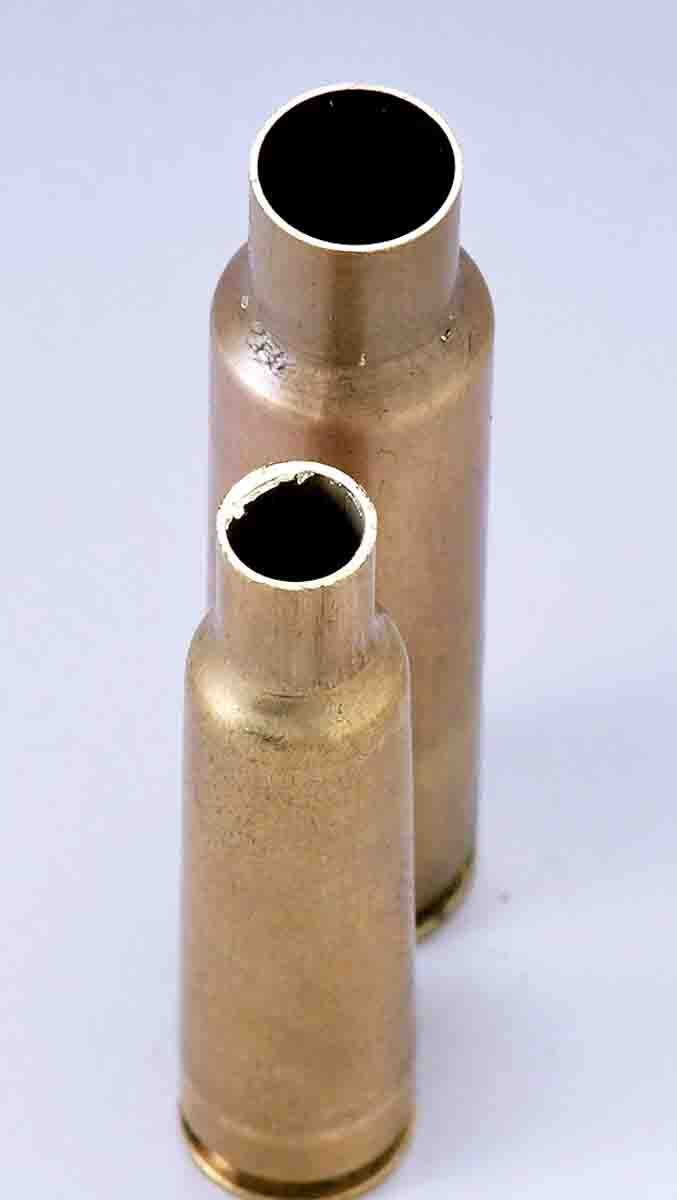
The .22-250 Remington case in the front was shortened in a form-and-trim die and finished with a file. The .350 Jamison case in the back was cut with the Mini Cut-Off Saw. Note the burrs resulting from the form-and-trim die that do not occur with the saw.
to take the tedium out of case length setup. Simply clamp the block in the vise, insert a case then adjust and lock the bolt to cut the proper case length. This is easier than trying to slide and clamp the block to a precise length.
I have used the block with only rimless rifle cases of a minimum taper. I do not know how square a cut would be with a rimmed case, for example, since the rim would tilt the case in the block cavity. Perhaps a sleeve could be made to slip over the case body and hold it squarely in the block.