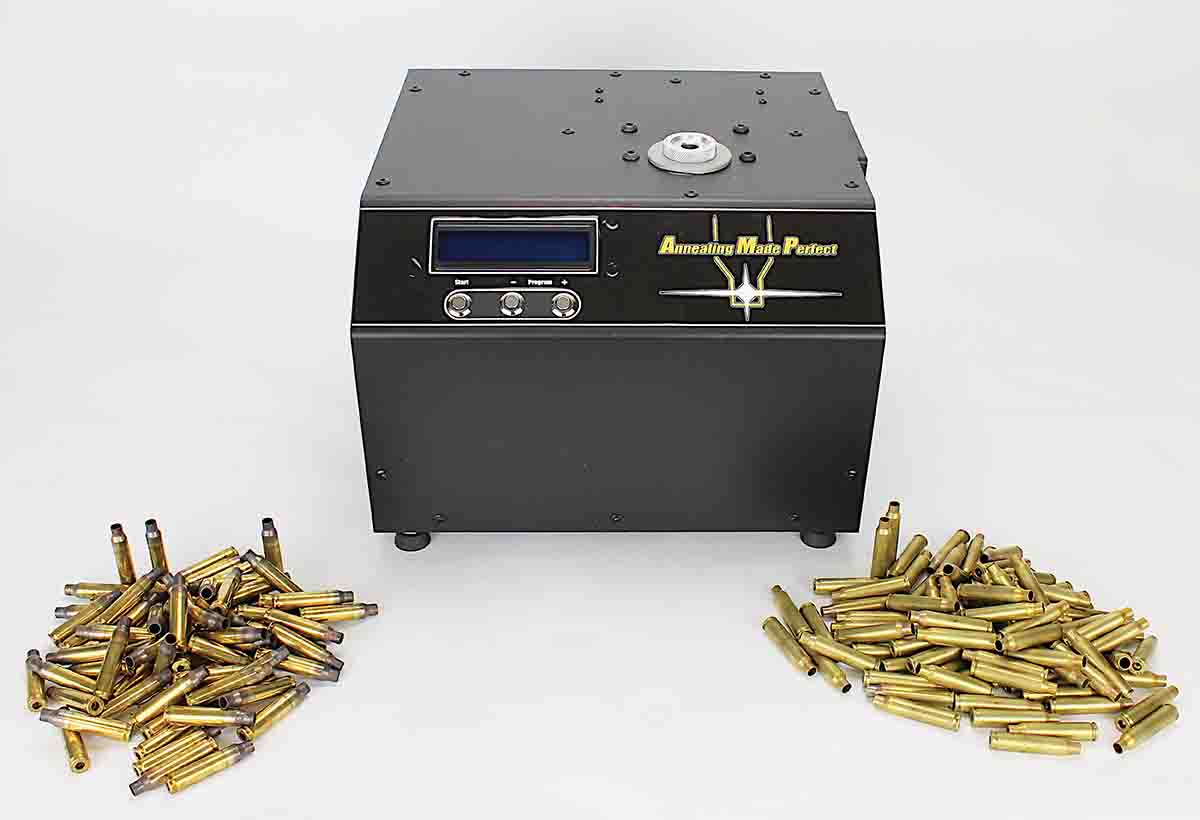
The AMP annealer utilizes computer-controlled induction heating to anneal brass.
Have you ever annealed cases by standing them in a pie pan of water and heating them with a torch? Welcome to the future. The Annealing Made Perfect machine from New Zealand introduces precision digital “plug & play” to case annealing – no propane torch required. But the pie pan is still handy.
In handloading’s context, annealing is heating a brass case at the neck/shoulder area in order to soften it. This, among other reasons, permits the case to more readily expand at that area to seal the chamber upon firing. That silver/blue tint visible at the neck and shoulder on new factory cases is the result of annealing (it is often more pronounced on military ammunition than on commercial ammunition). In handloading, repeatedly shooting and resizing cases “work-hardens” the brass – making it more brittle – until the case eventually cracks or splits at the neck or shoulder, either upon firing or resizing operations. Annealing postpones those case failures, sometimes indefinitely.
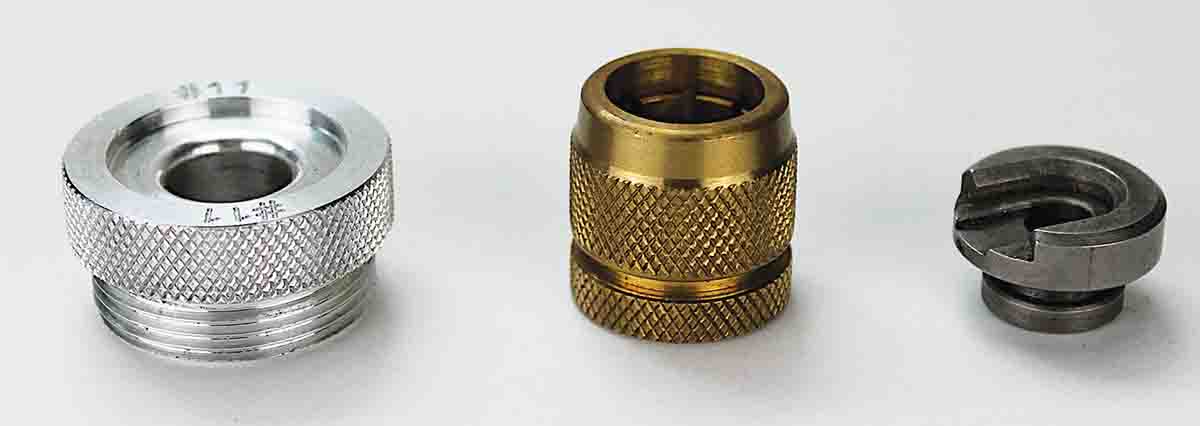
The only ancillaries needed for annealing are a cartridge-specific pilot (left) and a brass “grip” (center) for ordinary shellholders (right).
Most casual handloaders who work with common cartridges aren’t concerned with case annealing, but for those who engage in cartridge case conversions, or who reload expensive or hard-to-find brass, annealing is appealing. It especially benefits those in pursuit of the very highest degree of precision, such as long-range and benchrest competition shooters. Work-hardened brass “springs back” from the sizing die to varying degrees, which means cases aren’t sized consistently, which affects accuracy. For precision shooters/reloaders, the Annealing Made Perfect (AMP) machine leaves propane torches somewhere in the past with flint knives and bearskins, both in precise annealing and in the speed of operation. The AMP’s computer-controlled annealing precisely determines the optimum degree of annealing a given lot of cases should have, and it ensures consistent case-to-case-to-case neck tension on the bullet for more consistent velocity, and that, in turn, aids in promoting smaller groups at extended ranges.
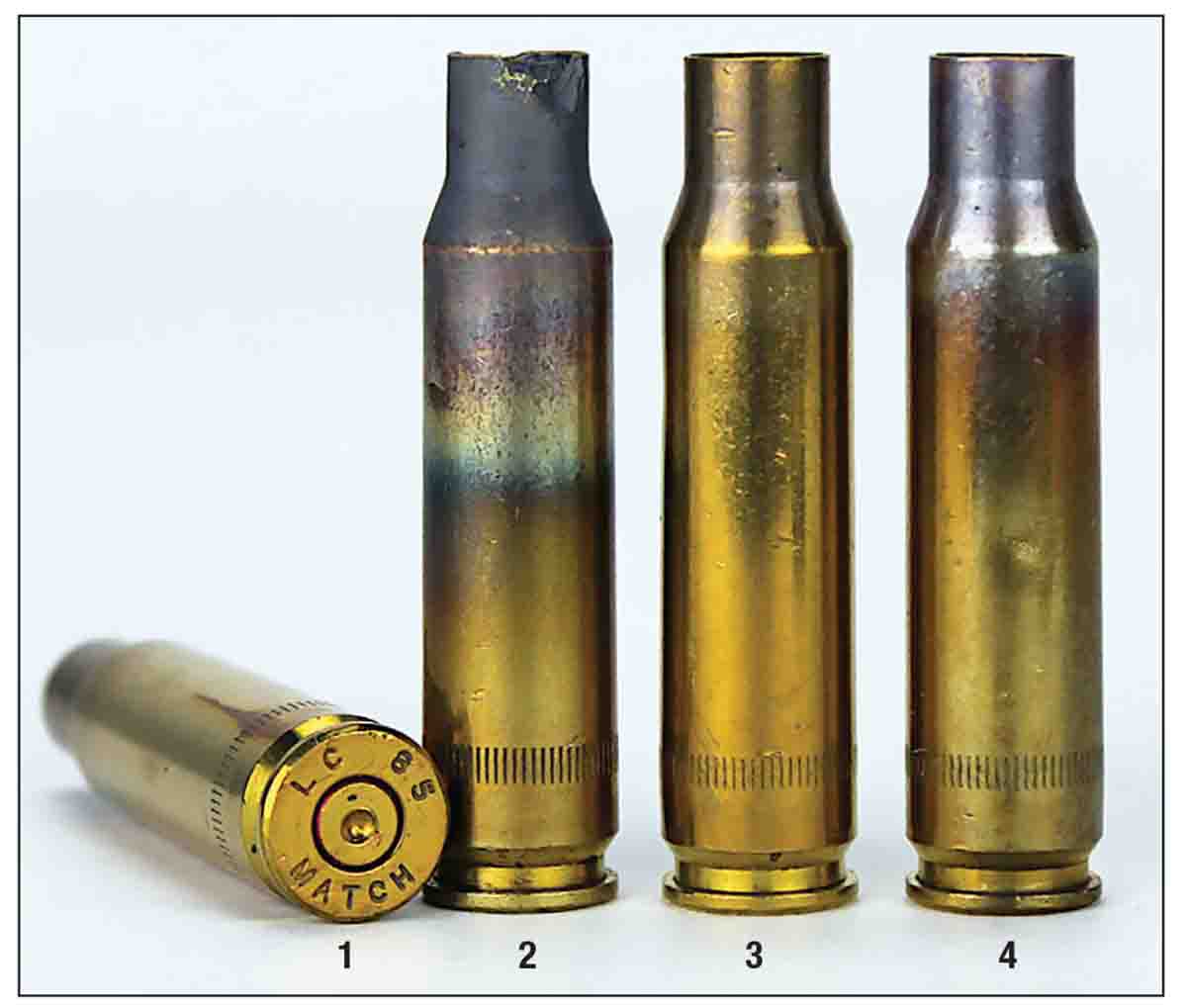
LC85 brass (1) shows a case sacrificed for analysis (2), an unannealed case (3) and an annealed case (4).
The AMP annealer works without flame by utilizing magnetic induction heating, the same principle as a kitchen induction stove. The simplest explanation is that electromagnets in the AMP annealer create a magnetic field oscillating at high frequency; inserting the brass case into that field creates eddy currents in the brass, and the resistance of the brass to the eddy currents causes the brass to heat. The AMP machine is about the size of a breadbox, anneals a case in about 3 seconds, and the only noise the AMP annealer makes, is the quiet whir of the cooling fans.
Featuring only three control buttons and a simple display, using the AMP annealer is refreshingly simple for the curmudgeonly who believe advancing high technology should have remained peaked a few more decades at the pinball machine. Plug it in, turn it on, select your program code, install the proper pilot, insert the case into the machine and press START. That’s it. Three seconds later, the case is annealed. Drop the hot case into the pie pan, insert the next case and press START.
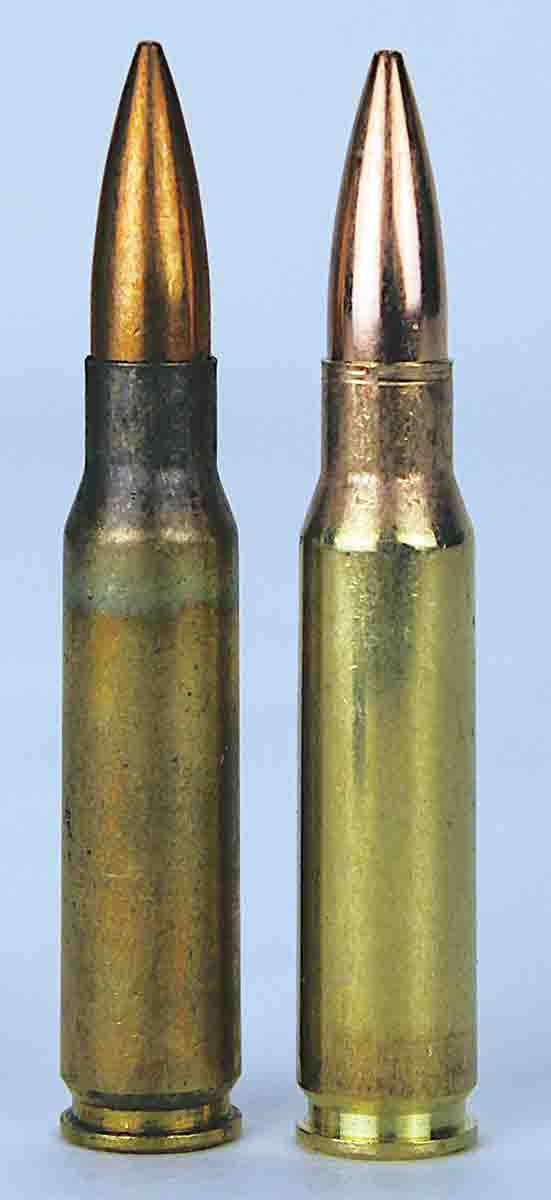
The factory annealing of a military 7.62x51 NATO cartridge (left) is more visible than on a commercial 308 Winchester cartridge (right).
The AMP annealer’s advantages over other annealing methods are numerous. There are no dangerous open flames or hissing propane tanks to cause the missus anxiety or needing replacement. No belts or cogs or moving parts that require lubrication or adjustment. No guessing whether cases may actually receive too much or too little annealing. A small footprint, and except for separate case pilots, self-contained. First and foremost, however, is that the AMP annealer applies precisely the correct amount of computer-controlled annealing, with repeatable consistency.
To illustrate, while a Winchester Model 1894 Trapper in 30-30 works, you won’t see one in a 600-yard match because it isn’t precise. Similarly, heating brass with a torch works, but it isn’t precise because brass cases aren’t manufactured to exactly the same thickness, even from lot to lot, there are variations. Brass thickness at the neck and shoulder is the deciding factor on how much heat must be applied for effective annealing without overdoing it. The human Mark I Mod 0 eyeball estimating the color of flame-heated brass, even when employing Tempilaq, cannot match computer analysis and control for precise annealing.
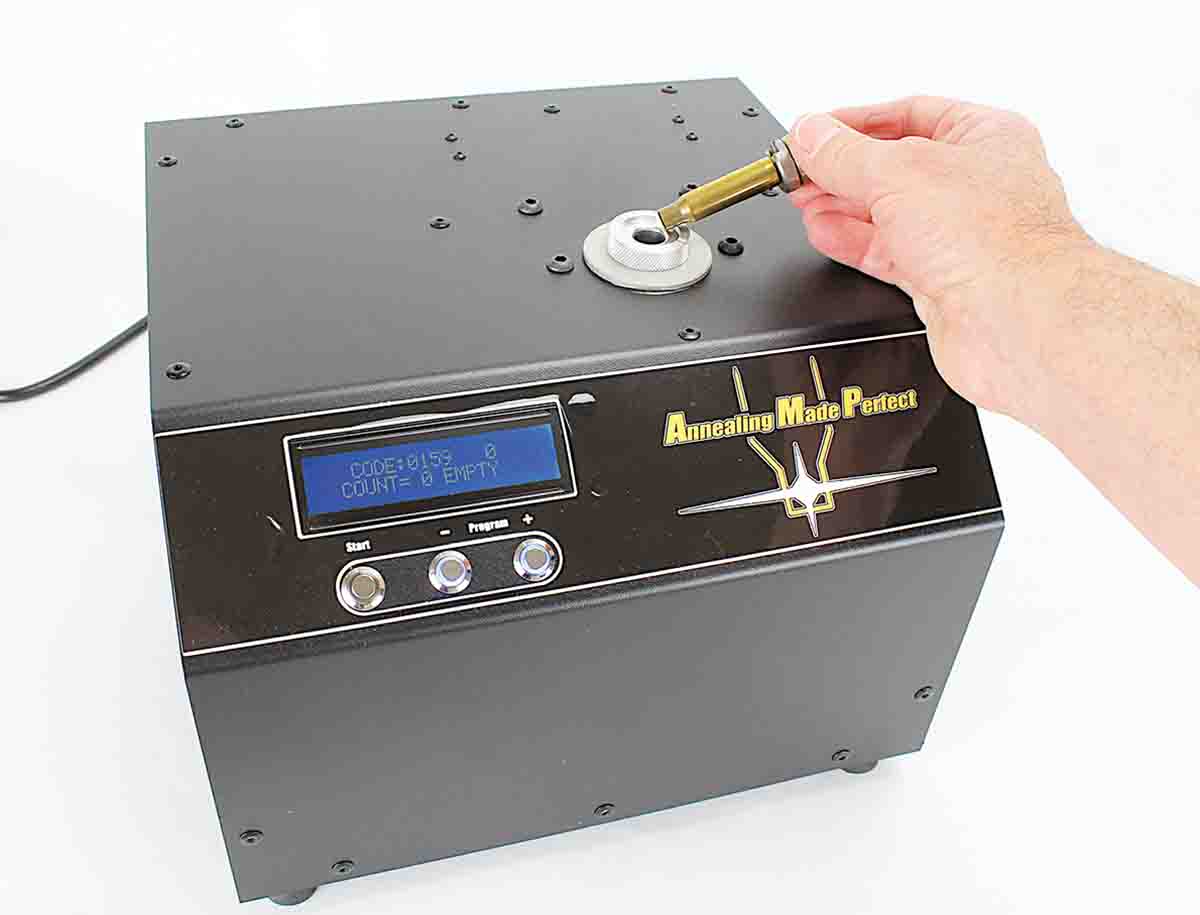
About the size of a breadbox, the computer-controlled AMP annealer outperforms all other methods of annealing. Insert a case and it’s annealed in 3 seconds – without flame.
When AMP annealers first hit the market in 2016, reloaders would send a sampling of cases to the factory; the factory would determine the proper annealing for that sample at no charge and send the reloader the proper code to enter into his AMP machine. Reloaders still send in cases, and results are posted on the AMP website that now has program settings for hundreds of cartridges that owners can utilize. But mailing cases to New Zealand is no longer necessary. Today, AMP’s AZTEC software can determine optimum annealing by sacrificing one case, which the machine essentially bakes to death during analysis.
Using the 308 Winchester as an example, after analyzing the sacrificial case, the AMP annealer displays a code number for that case, which the reloader uses to program the AMP annealer for his run of 308 Winchester cases. Brass from different manufacturers will differ significantly. But because the analysis is so precise, AZTEC can essentially detect variables in brass dimension in different lots of the same make of brass, so the reloader can program their AMP annealer to perfectly anneal cases on a lot number-to-lot number basis. For example, here I sacrificed one of each of the following 7.62x51 NATO and commercial 308 Winchester cases to AZTEC analysis with the results found in the table at the end of this article.
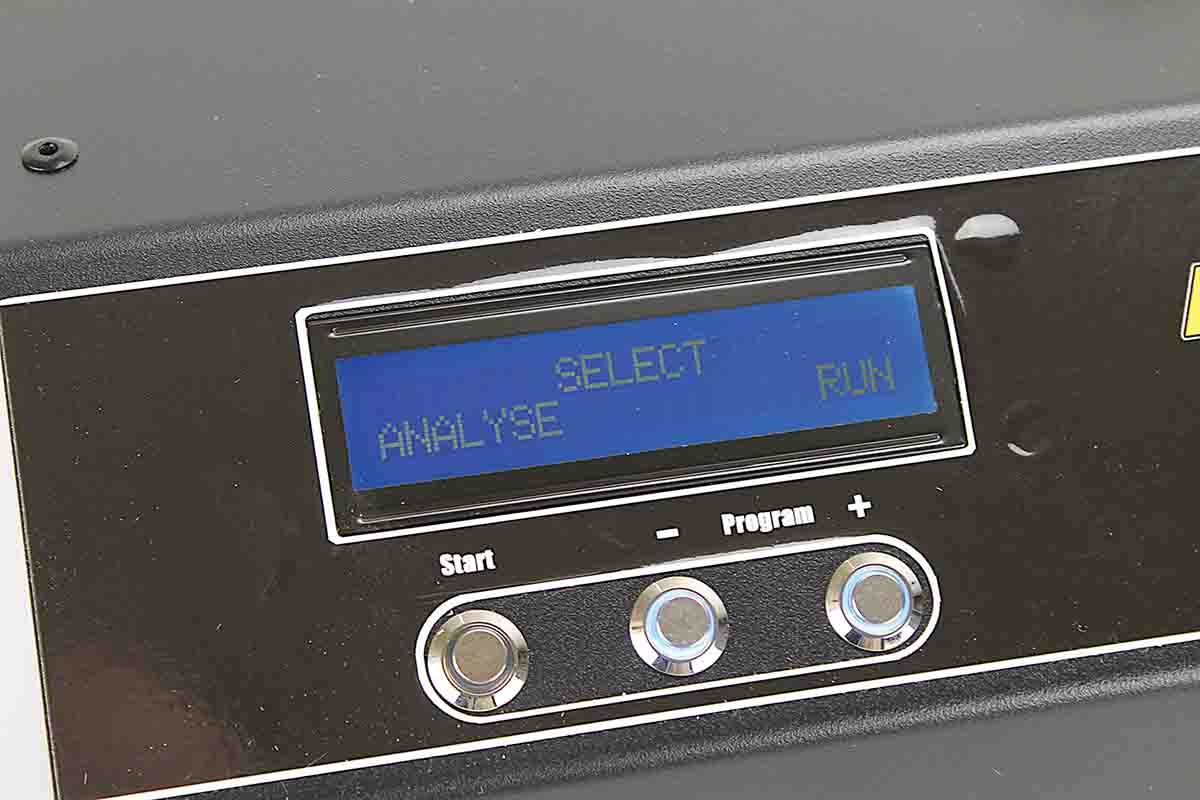
Selecting “ANALYSE” sacrifices one case for analysis.
While a one-step difference in code numbers indicated only a tiny difference between the brass cases, these spreads reveal significant differences in the thickness at the neck/shoulder area of these cases, for which the AMP annealer compensates. Now to anneal, say, my LC85 (Lake City 1985) cases over and over again, I program 0159 into the AMP machine before I start; for the Berger brass, 0164.
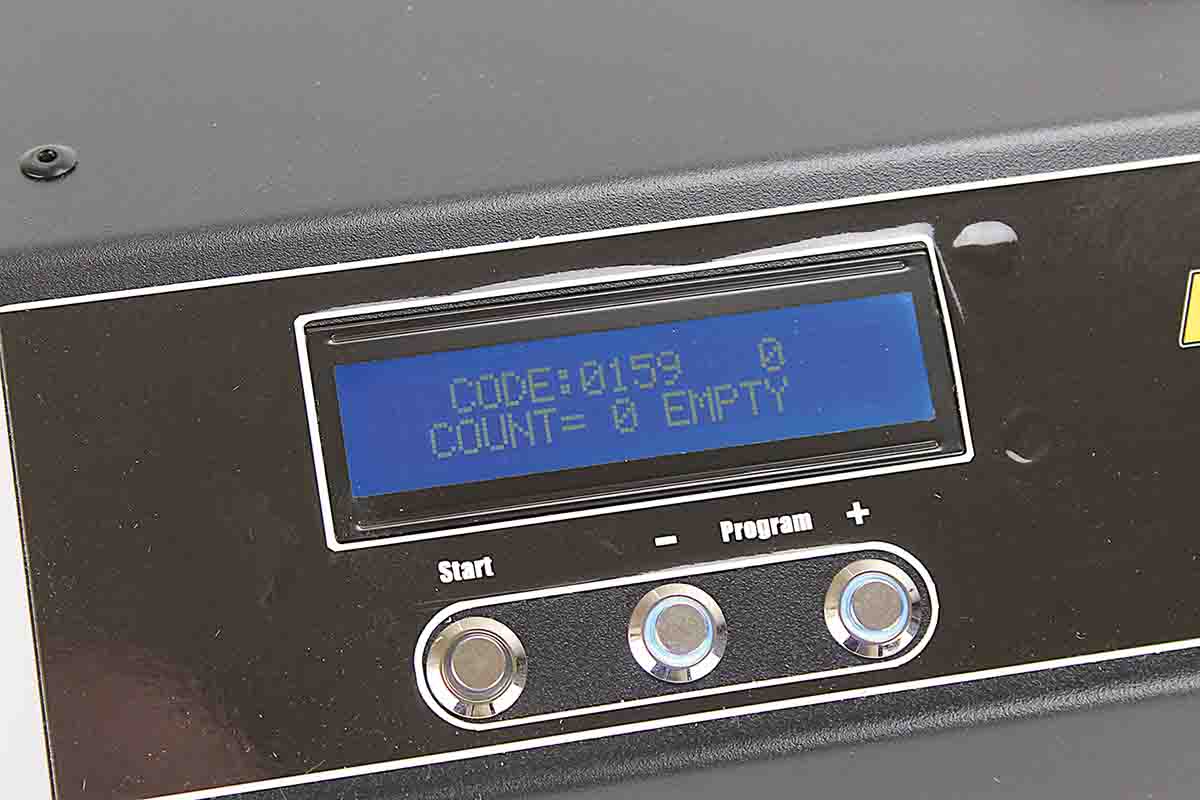
Once a case has been analyzed, the computer program code number (0159) is issued for that lot of brass. Record the code number and enter it for future annealing of that same lot, no need to sacrifice another case.
Beyond the annealer itself, the only ancillaries required are that pie pan, the appropriate common shellholder from your reloading press, a brass “grip” for the shellholder to protect fingers from hot brass and the aluminum pilots needed for specific cases or classes of case, the latter two provided by the AMP company. The pilot for 308 Winchester used here will also work with other cartridges based on the same case, such as 243 Winchester, 260 Remington and 7mm-08. Some other pilots have applications for several different cartridges, as well. The pilots differ in height to hold the cases in the correct place in the machine’s magnetic field.
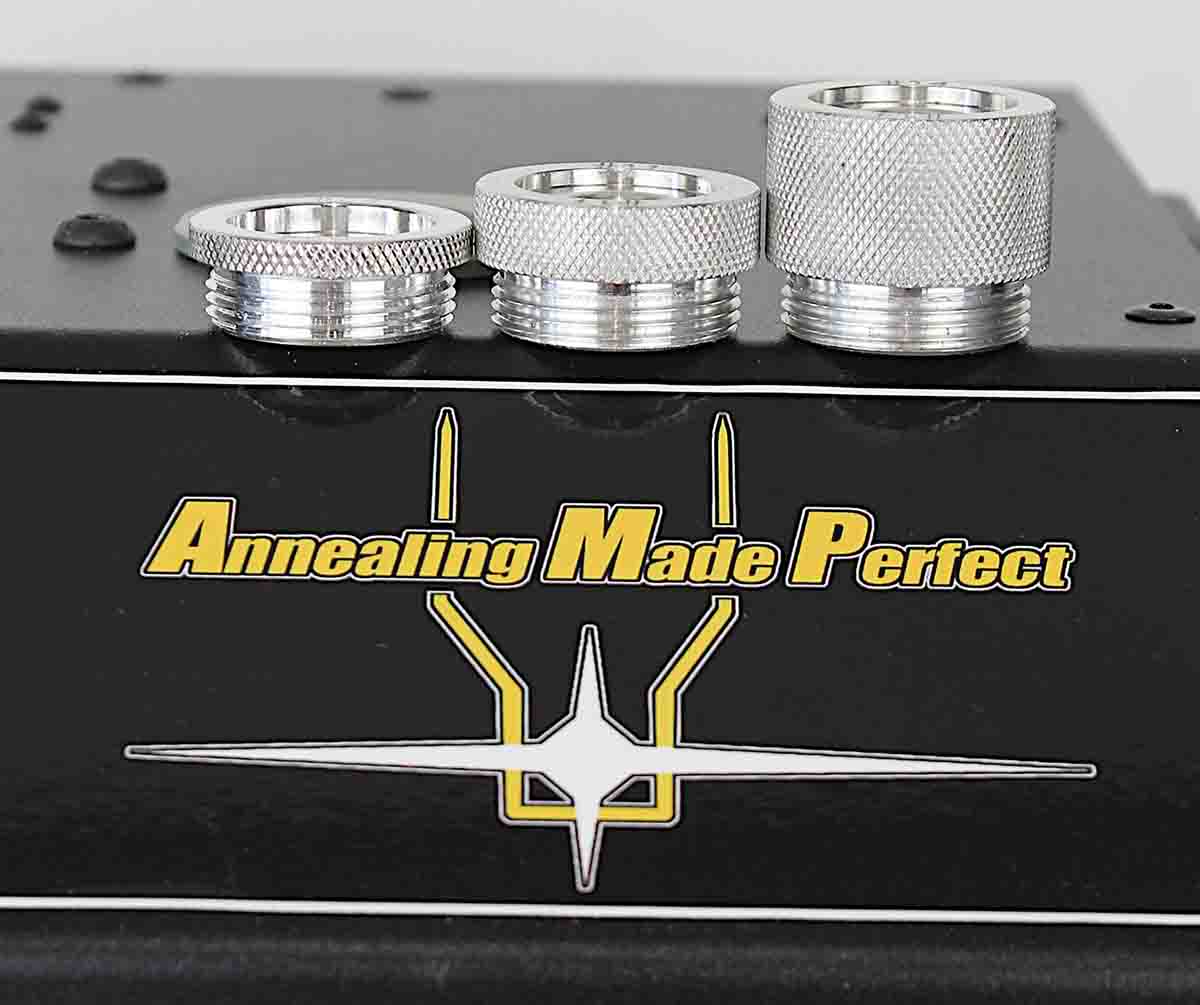
Pilots hold different cases at the proper depth in the oscillating magnetic field for precise annealing.
AMP’s present annealer incarnation is the Mark II, which can anneal cases in size from 17 Hornet to 50 BMG and has AZTEC pre-installed. The AMP annealer presented here is the original Mark I version I’ve been using for several years, released before AZTEC, and which cannot accommodate the largest cases like 50 BMG. Connecting the Mark I AMP annealer via a USB cable to my computer allowed me to download AZTEC when the program became available. Also introduced later, for the high-volume shooter an optional automatic case feeder utilizing a hopper is available for additional cost.
Mark II AMP machines and pilots are available from Creedmoor Sports (CreedmoorSports.com) or from AMP’s website for $1,595; pilots run from $19.95 to $25.95, depending on the cartridge. There’s a lot more information on the AMP website (AmpAnnealing.com), including some interesting reading on brass metallurgy and annealing, as well as instructional videos.